Checking out the Benefits of Sublimation Printing for High-Quality Fabrics
The Surge of DTF Printing: Exploring Its Advantages and Applications
The emergence of Straight to Film (DTF) printing modern technology is changing the custom-made garments industry, offering notable advantages and a broad array of applications. As the hunger for personalized items continues to broaden, recognizing how DTF printing can fulfill these developing needs is significantly vital.

Comprehending DTF Printing Modern Technology
Understanding DTF Printing Technology notes a significant advancement in the fabric printing market, particularly for its adaptability and performance. Direct-to-Film (DTF) printing is a sophisticated process that involves printing designs onto unique transfer films, which are then transferred onto fabric using warmth and pressure. Unlike conventional techniques, DTF printing does not need pre-treatment of the fabric, enabling a more streamlined workflow.

As soon as cured, the movie is positioned onto the textile, and a warmth press transfers the style by applying regular warm and pressure. This causes dynamic, high-quality prints that adhere perfectly to numerous material kinds, consisting of cotton, polyester, and blends (heat transfer vinyl printing). The modern technology's capacity to generate elaborate and dazzling designs with marginal setup makes it a game-changer in the textile printing field
Secret Benefits of DTF Printing
One of the key benefits of DTF printing is its outstanding adaptability, which enables for top notch prints on a large array of fabric types. This ability extends past typical cotton to consist of polyester, nylon, leather, and even combined materials, making it perfect for diverse textile applications. This versatility lowers the need for several printing technologies, simplifying production procedures and lowering overall prices.
An additional significant advantage is the superior print top quality that DTF technology delivers. By using lively, durable inks and specific application methods, DTF prints preserve their shade integrity and sharpness even after various washes. This results in an item that not only looks professional but likewise stands the test of time, offering regular value to both end-users and suppliers.
Furthermore, DTF printing provides a streamlined workflow, which can bring about increased efficiency and productivity. Unlike typical approaches such as screen printing, DTF does not need complicated setup or substantial drying out times. This convenience of use makes it an eye-catching choice for businesses of all sizes, enabling quicker turnaround times and the ability to deal with little to big manufacturing keeps up very little hassle.
Applications in Custom Clothing
In the world of custom-made clothing, DTF printing stands apart as a game-changing innovation that makes it possible for manufacturers and developers to create bespoke clothes with unrivaled detail and high quality. Direct-to-film (DTF) printing has revolutionized the customized garments sector by using flexibility in style, vivid shade recreation, and toughness. This ingenious approach allows for intricate designs to be moved onto a large array of fabrics without compromising the honesty of the product.
One considerable application of DTF printing remains in creating custom tee shirts, hoodies, and sports apparel. The ability to publish intricate graphics with fine information and gradients makes it optimal for personalized apparel, such as team uniforms and marketing product. DTF printing is especially helpful for one-off items and limited-run orders, providing a reliable and cost-efficient visit the site service compared to conventional display printing approaches (screen printing).
Additionally, DTF printing has opened up new opportunities for fashion developers to try out one-of-a-kind patterns and appearances, making it possible for the creation of cutting-edge, avant-garde collections. This modern technology also sustains local business and independent artists by lowering the barriers to access in the custom clothing market. Eventually, DTF printing is improving the landscape of customized garments, merging artistic expression with technological improvement.
Flexibility Throughout Different Materials
Building on the improvements in personalized clothing, DTF printing's flexibility throughout various materials additionally improves its allure. Unlike conventional printing approaches, DTF (Direct-to-Film) printing can be used to a substantial array of substratums, consisting of cotton, polyester, blends, leather, and also hard surface areas like wood and glass.
The capability to publish on varied products opens up numerous opportunities for organizations across various sectors. As an example, in the promotional items sector, companies can customize a large selection of things, from lug bags and caps to cups and phone cases, all with the exact same printing modern technology. In the garment industry, look at this now DTF printing allows developers to experiment with intricate patterns and lively colors on unique materials, pressing the limits of creativity.
In addition, DTF printing's compatibility with various materials also translates to cost-efficiency and reduced waste, as manufacturers can utilize the same equipment for several applications. This flexibility not only broadens the scope of item offerings however also enhances functional performance.
Future Potential Customers of DTF Printing
As the marketplace evolves, the future potential customers of DTF printing are positioned to reinvent numerous markets with continuous advancement and technical advancements. The surge popular for tailored apparel and advertising items is driving the need for more efficient, functional, and economical printing approaches. DTF printing, with its ability to generate high-grade, long lasting prints on a large range of materials, stands at the leading edge of this transformation.
Arising trends show that DTF printing will significantly integrate with automation and AI modern technologies, enhancing manufacturing speed and lowering labor prices. Advanced software program solutions will certainly even more optimize design accuracy, shade matching, and print consistency, resolving some of the existing constraints. In addition, environmentally friendly inks and recyclable transfer movies are anticipated to acquire grip, straightening with worldwide sustainability objectives.
As research study and advancement initiatives continue to expand, the range of DTF printing will likely widen, opening up new avenues for innovative and commercial applications. In recap, the future of DTF printing is intense, appealing substantial improvements and broader sector adoption.
Conclusion
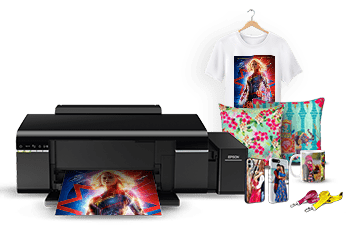
Understanding DTF Printing Innovation marks a considerable advancement in the fabric printing market, specifically for its adaptability and effectiveness. Direct-to-Film (DTF) printing is an innovative process that entails printing styles onto special transfer movies, which are after that transferred onto textile utilizing heat and pressure. DTF printing is especially useful for one-off items and limited-run orders, offering a economical and efficient service compared to conventional screen printing methods.
Unlike standard printing methods, DTF (Direct-to-Film) printing can be used to a substantial variety of substrates, including cotton, polyester, blends, natural leather, and also tough surfaces like wood and glass.DTF printing innovation is transforming the personalized clothing market by supplying reliable, economical, and functional solutions for producing dynamic styles on numerous fabrics without pre-treatment.